12/08/2024
How to Maximize Your CNC Turning Center Machine?
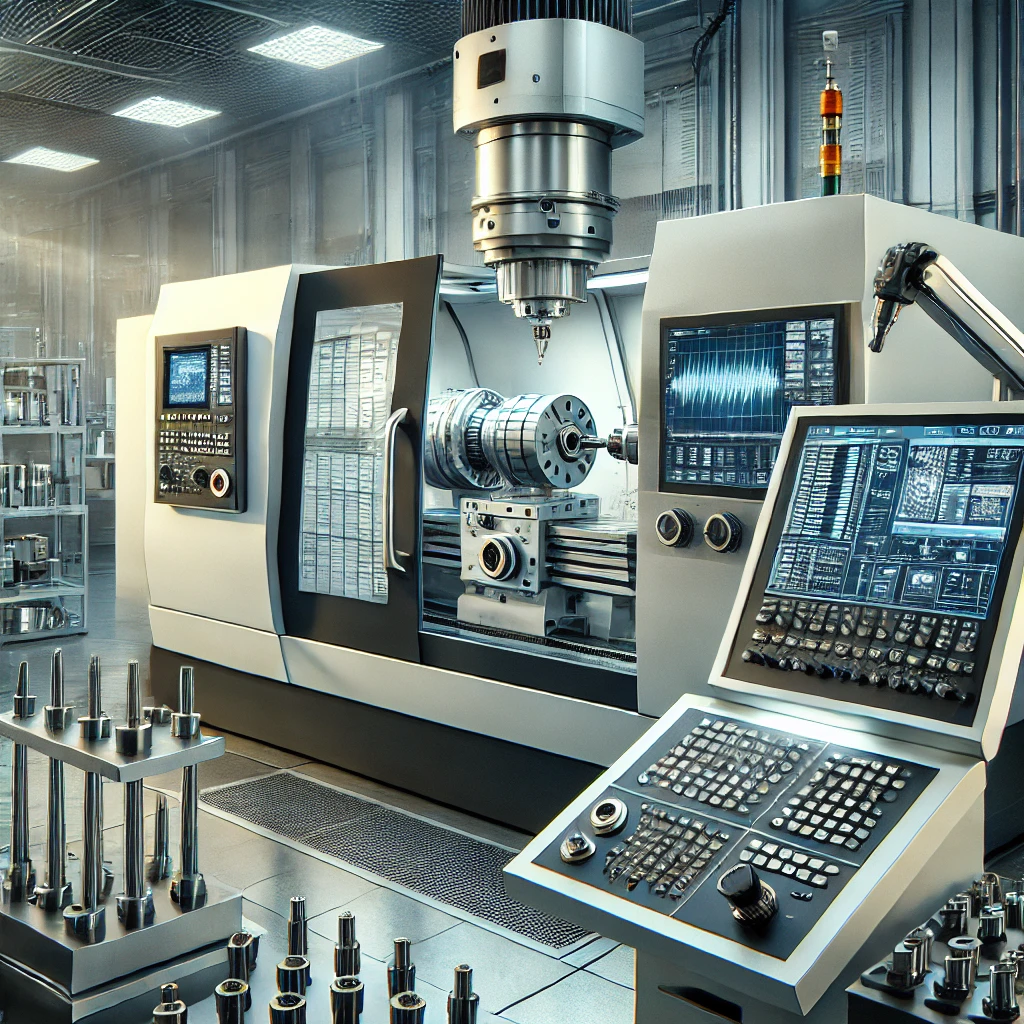
Maximizing the performance of your CNC Turning Center involves optimizing several aspects of its operation, from tooling and programming to maintenance and setup. Here’s a technical guide to help you enhance the efficiency, precision, and longevity of your CNC Turning Center:
1. Optimize Tooling and Tool Management
- High-Quality Cutting Tools: Use high-quality, coated cutting tools tailored for the material being machined. Coatings such as TiAlN, TiN, or diamond-like carbon (DLC) can increase tool life and allow for more aggressive cutting parameters.
- Tool Holders: Ensure that tool holders are balanced and free from wear. Precision tool holders reduce runout, which improves surface finish and dimensional accuracy.
- Tool Length Minimization: Shorter tool setups minimize deflection and vibration, leading to better surface finishes and increased tool life.
- Automatic Tool Changers (ATC): Utilize the ATC feature effectively by organizing tools in the changer to minimize tool change time and tool travel distance.
- Tool Monitoring Systems: Implement tool monitoring systems to detect wear or breakage, allowing for timely replacements and reducing machine downtime.
2. Enhance Programming Techniques
- Advanced CAM Software: Use advanced CAM software to generate optimized tool paths that minimize non-cutting movements and reduce cycle times.
- Adaptive Machining: Utilize adaptive machining strategies that adjust feed rates and spindle speeds in real-time based on the actual cutting conditions, improving both tool life and machining accuracy.
- High-Efficiency Turning: Implement high-efficiency turning (HET) strategies to optimize cutting conditions, reduce cycle times, and extend tool life by maintaining a constant chip load.
- Reduce Air Cutting: Minimize air cutting (non-cutting tool movements) in the program to reduce unnecessary time spent on non-productive motions.
- Sub-Spindle Programming: If your turning center has a sub-spindle, optimize the programming to utilize both spindles effectively, reducing part handling and cycle times.
3. Improve Machine Setup and Calibration
- Precision Workholding: Use precision chucks, collets, or fixtures that provide accurate and repeatable workholding. Ensure that workpieces are properly aligned and secured to avoid runout or misalignment.
- Tailstock and Steady Rest Optimization: When machining long parts, ensure that the tailstock or steady rest is correctly positioned and adjusted to avoid deflection.
- Probing Systems: Use in-machine probing systems for automatic part alignment, tool setting, and in-process inspection. This reduces setup time and ensures accuracy.
- Thermal Stability: Ensure the machine is thermally stable before beginning precise machining operations. Some machines have built-in thermal compensation systems to adjust for temperature fluctuations.
4. Maximize Spindle Utilization
- High-Speed Machining: For applicable materials, utilize high-speed machining techniques to increase material removal rates while maintaining accuracy.
- Spindle Warm-Up: Always perform a spindle warm-up routine before starting high-speed operations to avoid thermal shock and extend spindle life.
- Balanced Workload: Schedule workloads to balance spindle usage across shifts, avoiding excessive wear from overuse.
5. Optimize Coolant and Lubrication Systems
- High-Pressure Coolant Systems: Use high-pressure coolant systems to improve chip evacuation, reduce heat generation, and allow for more aggressive cutting parameters.
- Coolant Management: Regularly monitor and maintain coolant levels, concentration, and cleanliness to ensure consistent cooling and lubrication performance.
- Through-Tool Coolant: If available, use through-tool coolant to deliver coolant directly to the cutting edge, especially for deep hole drilling or high-speed operations.
6. Implement Preventive Maintenance
- Scheduled Maintenance: Adhere to a strict maintenance schedule that includes lubrication, filter changes, and inspection of key components like ball screws, linear guides, and bearings.
- Vibration Analysis: Regularly conduct vibration analysis to detect early signs of mechanical issues, such as bearing wear or misalignment, before they lead to significant downtime.
- Alignment Checks: Periodically check and adjust machine alignment, including headstock, tailstock, and turret alignment, to ensure precision machining.
- Laser Calibration: Use laser calibration tools to check and adjust the machine’s positioning accuracy and repeatability.
7. Utilize Advanced Machine Features
- Live Tooling: If your CNC turning center is equipped with live tooling, maximize its use by integrating milling, drilling, and tapping operations into your turning cycles. This reduces the need for secondary operations on other machines.
- Y-Axis and Sub-Spindle Capabilities: Utilize Y-axis and sub-spindle capabilities to perform more complex operations, such as off-center milling or multi-sided machining, without repositioning the workpiece.
- C-Axis Programming: For machines with a C-axis, take advantage of its capabilities to perform operations like contour milling and drilling at various angles, increasing part complexity without additional setups.
8. Data-Driven Optimization
- Machine Monitoring Systems: Implement machine monitoring systems to track spindle utilization, cycle times, and downtime. Analyzing this data can help identify inefficiencies and opportunities for improvement.
- OEE (Overall Equipment Effectiveness): Calculate and analyze OEE to understand how effectively your turning center is being utilized and identify areas where productivity can be improved.
- Real-Time Feedback Loops: Use feedback loops between the CNC machine and your CAM system to adjust tool paths and machining parameters based on real-time performance data.
9. Training and Skill Development
- Operator Training: Ensure operators are fully trained on all aspects of the machine, including advanced programming techniques, tool management, and maintenance procedures.
- Cross-Training: Cross-train staff on different machines and processes to increase flexibility and reduce dependency on specific individuals.
10. Leverage Automation
- Robotic Automation: Integrate robotic arms for automatic loading and unloading of parts, reducing manual handling time and increasing spindle uptime.
- Bar Feeders: Use automatic bar feeders for continuous machining operations, minimizing downtime between part changes.
- In-Line Inspection: Implement automated in-line inspection systems to check part quality without stopping the machine, reducing scrap and rework.
By following these technical strategies, you can significantly enhance the performance, precision, and productivity of your CNC Turning Center, leading to higher-quality parts and more efficient operations.